10 - Non-premixed ammonia combustion in tailored ceramic porous inert media
Summary
The project focuses on the thermochemical energy conversion process of the carbon-free chemical energy carrier ammonia and of ammonia/hydrogen mixtures. Ammonia is considered as one of the future energy and hydrogen carriers, especially in terms of long-distance transport since its thermal properties are similar to those of propane and it can easily be liquefied for storage and transport with an established transportation network. However, the combustion of ammonia poses considerable challenges. The three major challenges are its low burning velocity compared to hydrocarbons resulting in poor flame stability, extremely high levels of nitrogen oxide formation and high toxicity even at trace levels. Conventional approaches to address these challenges are the addition of highly reactive fuels like hydrogen or methane to address the issue of flame stability, conversion in staged fuel rich/lean processes to address the high NOx formation and post treatment for avoiding unburnt ammonia emissions. We propose to address all challenges at once by a novel concept for non-premixed combustion of ammonia in Porous Inert Media (PIM). Combustion in PIM can increase burning velocities by more than one order of magnitude compared with non-PIM combustion due to heat recirculation through the solid phase. Heat recirculation combined with the thermal inertia of the solid phase resolves the issue of flame stability. The non-premixed approach results in high temperatures of the initial fuel rich or pure fuel streams decomposing ammonia without significant NOx formation, while the good mixing and temperature homogenization effects by the flow through the PIM lead to a complete burnout of remaining ammonia in a post-combustion zone. In order to realize such concept, tailored high temperature-resistant materials are required, both in terms of geometry as well as spatial distribution of thermal properties. Additive manufacturing (ADM) of PIM structures from composite ceramic materials is needed to control the process through customized properties regarding heat conduction, radiation properties, dispersion and the flow field. The fundamental research and design of the non-premixed PIM burner for ammonia and ammonia/hydrogen-mixtures requires a strong interdisciplinary research team in the fields of high-fidelity experiments for combustion in PIM (EXP, KIT), detailed pore-resolved numerical simulations (SIM, KIT) and additive manufacturing methods for thermal shock and corrosion-resistant functional components (ADM, TU BAF).
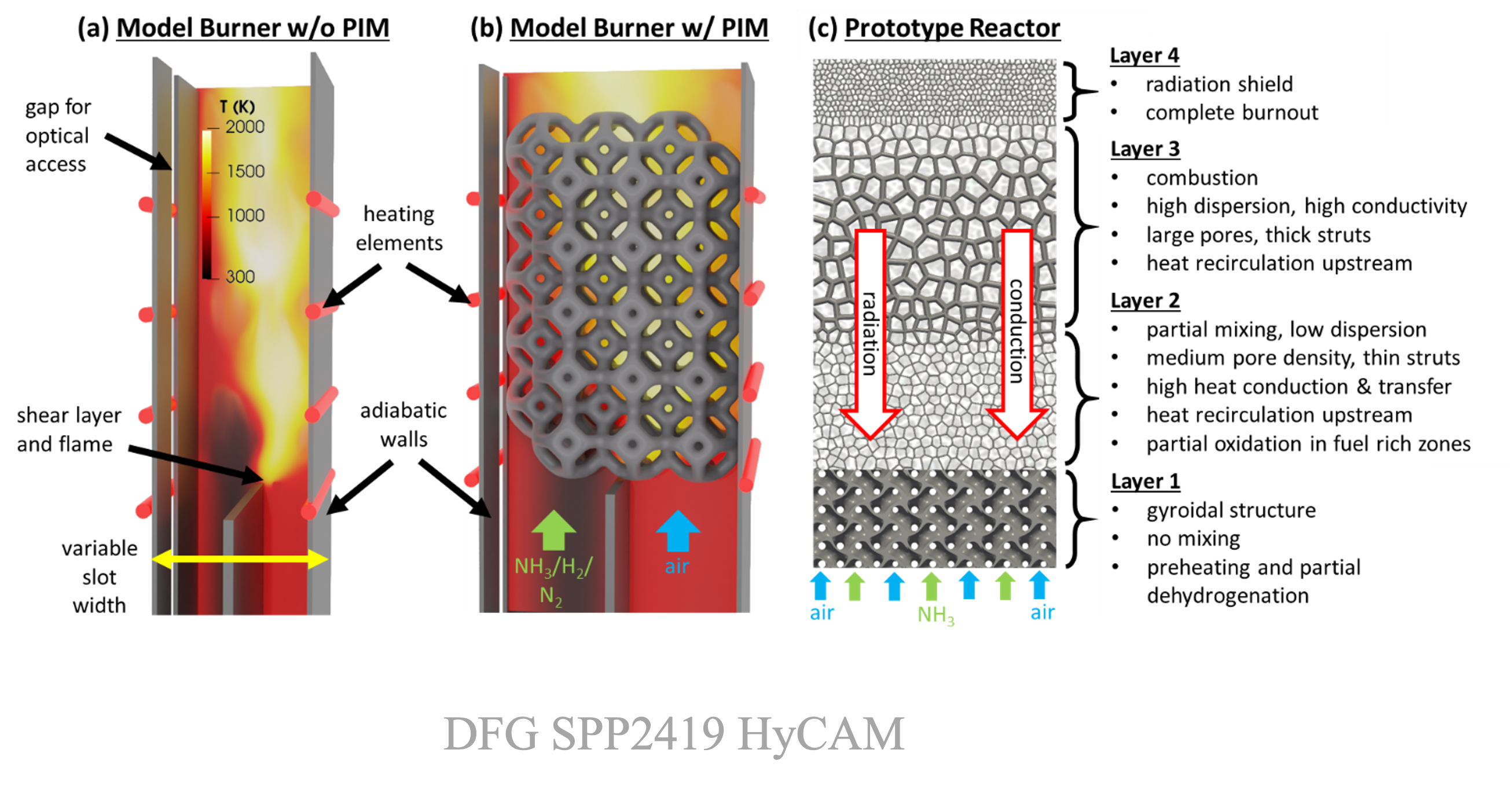
Research Team

Prof. Dr.-Ing. Dimosthenis Trimis
Principal Investigator (PI)
Karlsruhe Institute of Technology
Engler-Bunte-Institute
dimosthenis.trimis(at)kit.edu
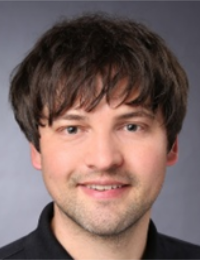
Prof. Dr. Oliver T. Stein
Principal Investigator (PI)
Karlsruhe Institute of Technology
Engler-Bunte-Institute
oliver.t.stein(at)kit.edu
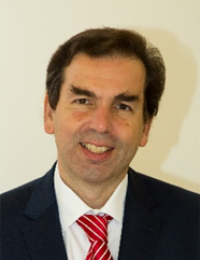
Prof. Dr.-Ing. habil. Christos G. Aneziris
Principal Investigator (PI)
TU Bergakademie Freiberg
Institute of Ceramics, Refractories and Composite Materials
Christos.Aneziris(at)ikfvw.tu-freiberg.de

Dr.-Ing. Nora Brachhold
Principal Investigator (PI)
TU Bergakademie Freiberg
Institute of Ceramics, Refractories and Composite Materials
Nora.Brachhold(at)ikfvw.tu-freiberg.de

Dr.-Ing. Björn Stelzner
Researcher
Karlsruhe Institute of Technology
Engler-Bunte-Institute
bjoern.stelzner(at)kit.edu

Dr.-Ing. Thorsten Zirwes
Researcher
University of Stuttgart
Institute for Combustion Technology
thorsten.zirwes(at)itv.uni-stuttgart.de

M.Sc. Daniel Kretzler
Doctoral Researcher
Karlsruhe Institute of Technology
Engler-Bunte-Institute
daniel.kretzler(at)kit.edu
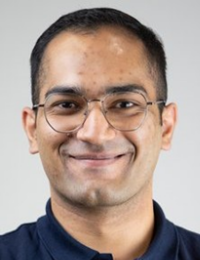
M.Sc. Rishabh Puri
Doctoral Researcher
Karlsruhe Institute of Technology
Engler-Bunte-Institute
rishabh.puri(at)kit.edu
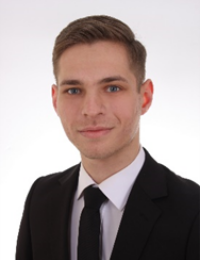